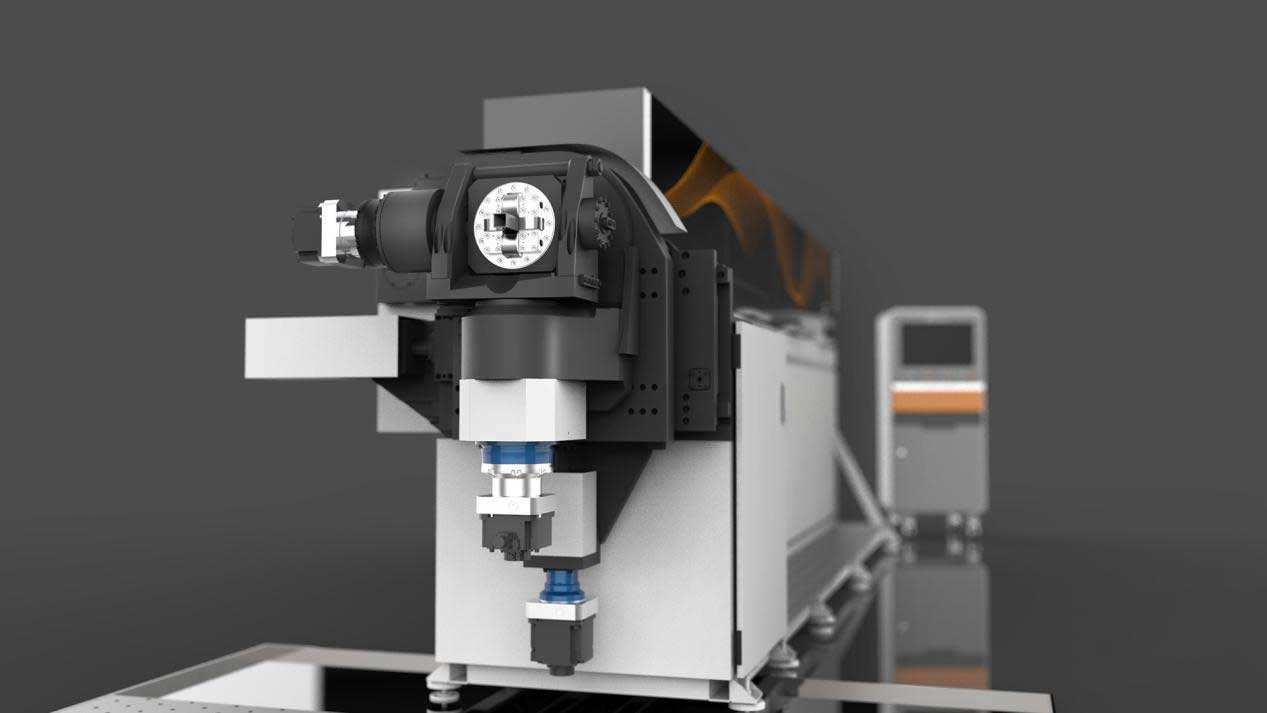
Three-axis and Six-axis 3D Freeform Bending Systems
Freeform Tube Bender
3D freeform tube bender with high forming accuracy and quality.
Accurate, die-less continuous bending forming of tubes, profiles, and wires,
particularly suitable for complex spatially shaped bent components or components with continuously varying bending radii.
WHAT IS FREEFORM TUBE BENDER?
Die-less forming, fast forming speed, high forming precision, and wide material adaptability.
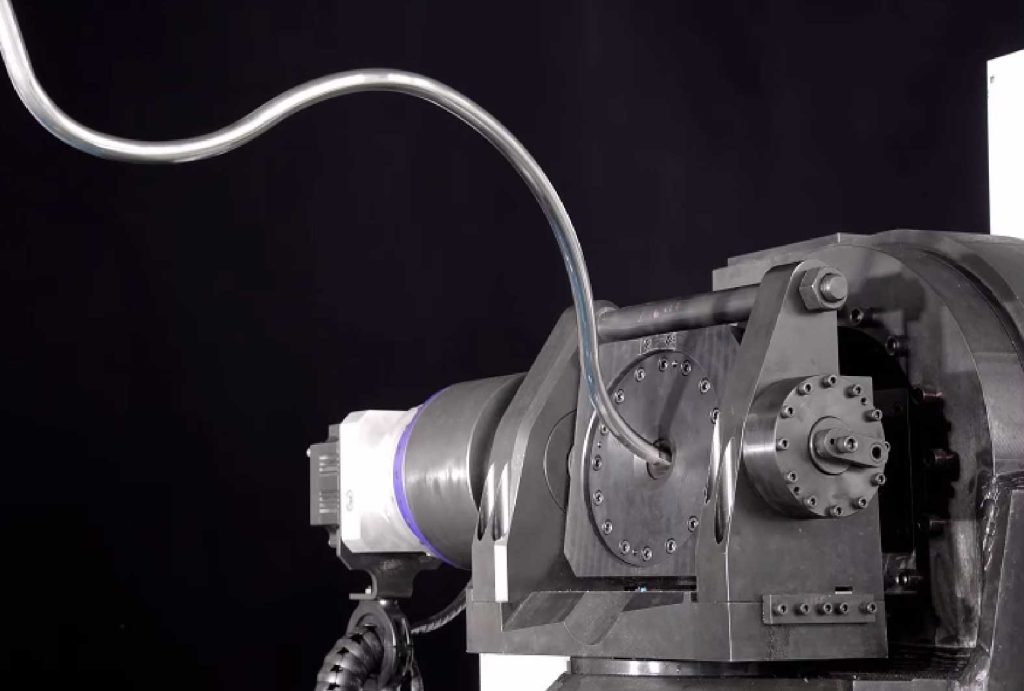
The 3D freeform bending technology is an emerging flexible, precise, and efficient method for bending pipes or tubes, profiles, and wires.
3D Freeform Tube Bender can achieve rapid and precise 3D forming of complex bent components for tubes and profiles. Compared to traditional bending methods, the freeform tube bender primarily achieves flexible and precise forming of hollow components by controlling the movement trajectory of the bending die in three-dimensional space, significantly improving the geometric accuracy and complexity of the components.
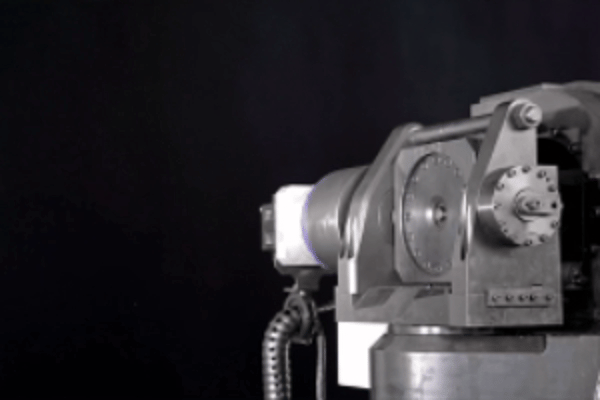
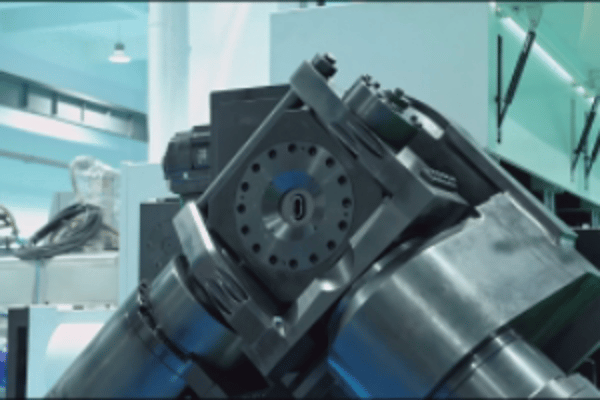
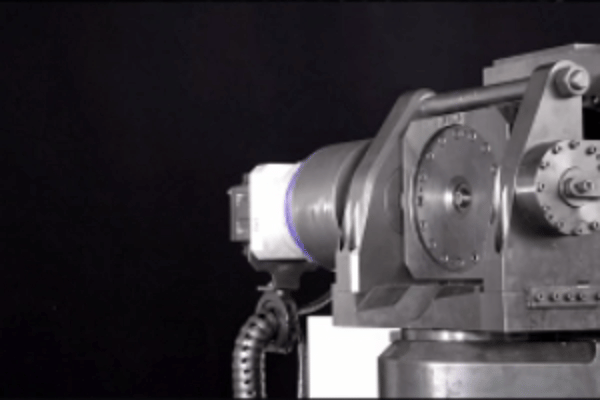
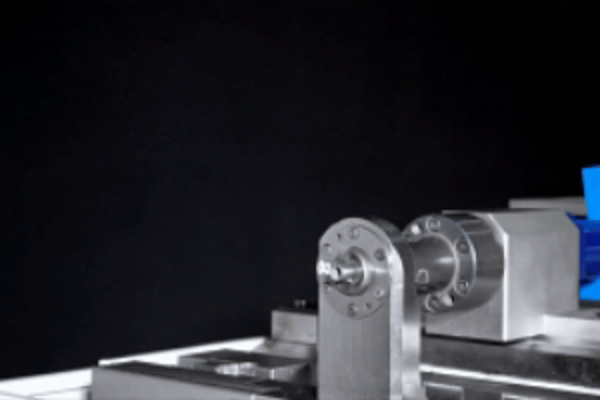
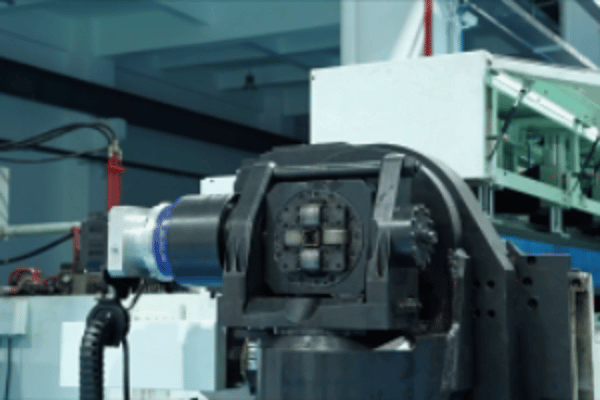
FREEFORM TUBES AND PROFILE BENDING OPEN UP POSSIBILITIES NEVER BEFORE POSSIBLE
TYPES OF FREEFORM TUBE BENDER
PBF 3D Freeform Tube Bender includes 3-axis, and 6-axis freeform bending systems, enabling flexible bending forming manufacturing of three-dimensional complex hollow components with various material systems and geometric features.
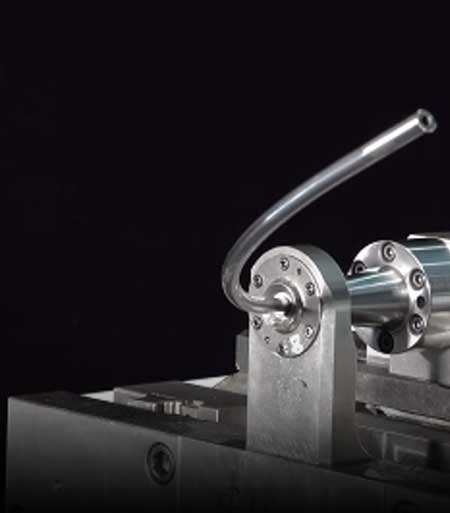
3-Axis Freeform Tube Bender
- X, Y, and Z axes: The X and Y axes are used for freeform bending, while the Z axis functions as the feed axis for the profiles.
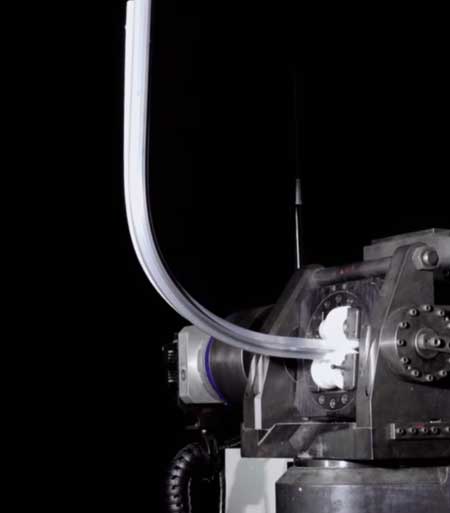
6-Axis Freeform Tube Bender
- X, Y, and Z axes: The X and Y axes are used for freeform bending, while the Z axis functions as the feed axis for the profiles.
- A, B, and C axes: Twist bending deformation for 3D freeform bending square, rectangular, and other non-circular irregular profiles (such as aluminum extrusions).
Standard Machine Model: Maximum processing tube blank length is 3000mm, customizable up to a maximum length of 6000mm, with increments of 1000mm for customization.
TECHNICAL PARAMETERS OF 3-AXIS
Model Description: PBF-T60, "T" denotes the three-axis freeform bending system, and "60" indicates the maximum processing tube diameter of 60mm (outer diameter of the tube).
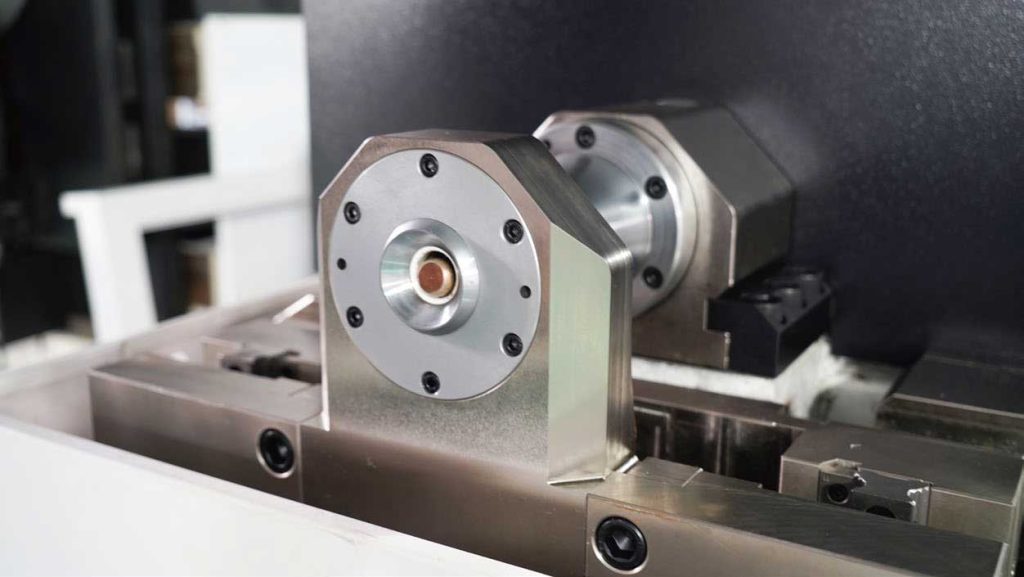
Technical Parameters | PBF-T30 | PBF-T60 | PBF-T90 |
Max Processing Tube Diameter | 8-32mm | 30-60mm | 60-90mm |
Max Bending Radius | ∞ | ∞ | ∞ |
Min Bending Radius | 3D | 3D | 3D |
Bending Angle | 0-360° | 0-360° | 0-360° |
Positioning Accuracy/Feed Axis | ≤0.05mm | ≤0.05mm | ≤0.05mm |
Positioning Accuracy/Bending Axis | ≤0.02mm | ≤0.02mm | ≤0.02mm |
Max Speed | 250mm/s | 250mm/s | 250mm/s |
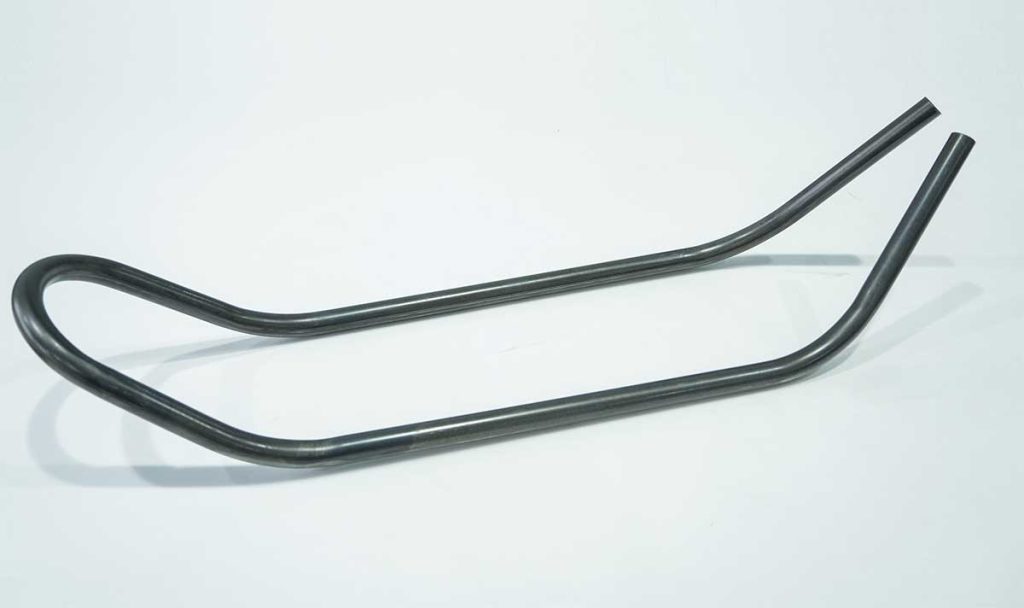
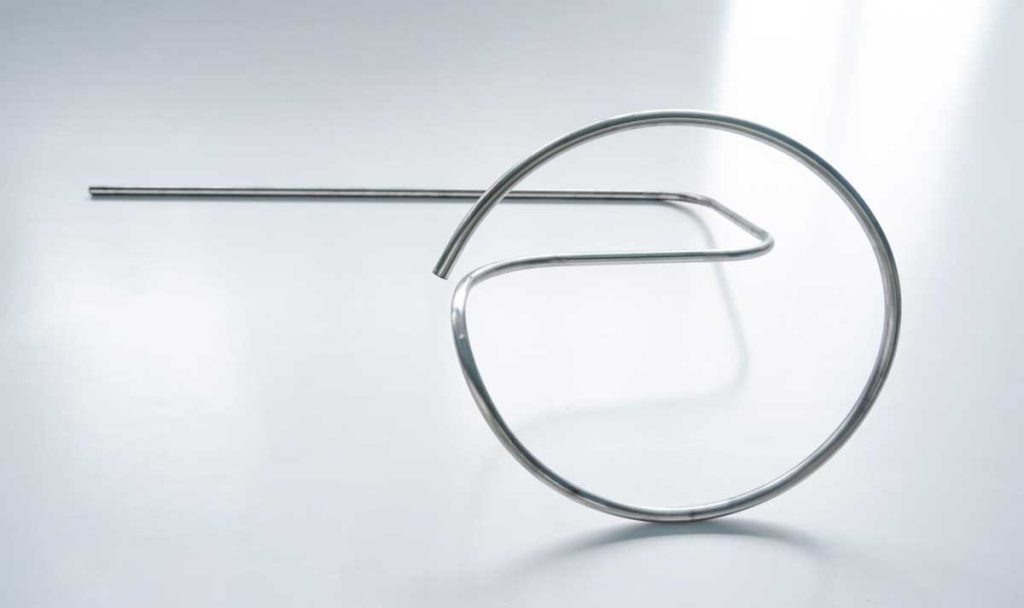
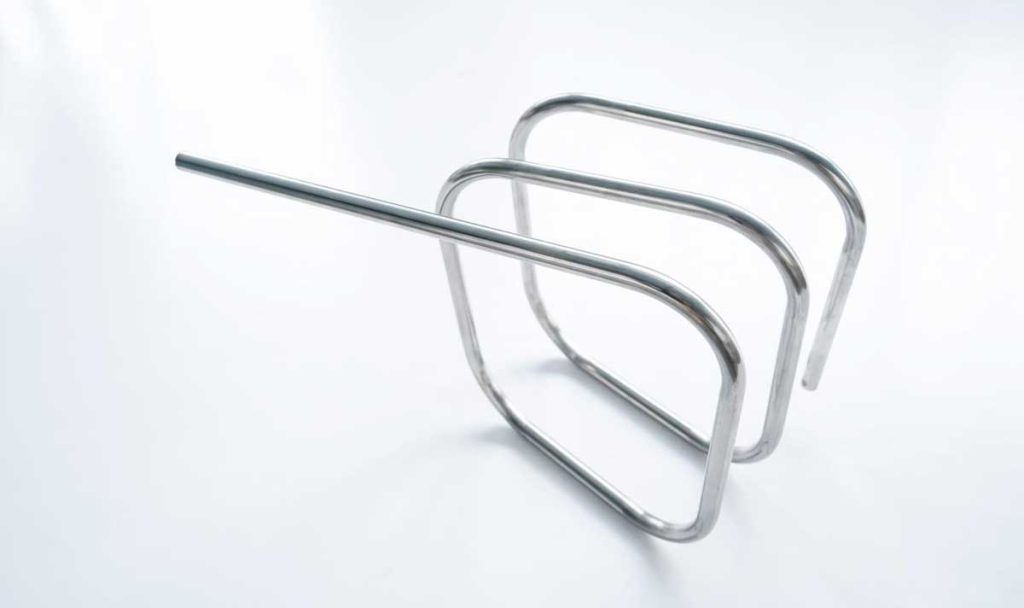
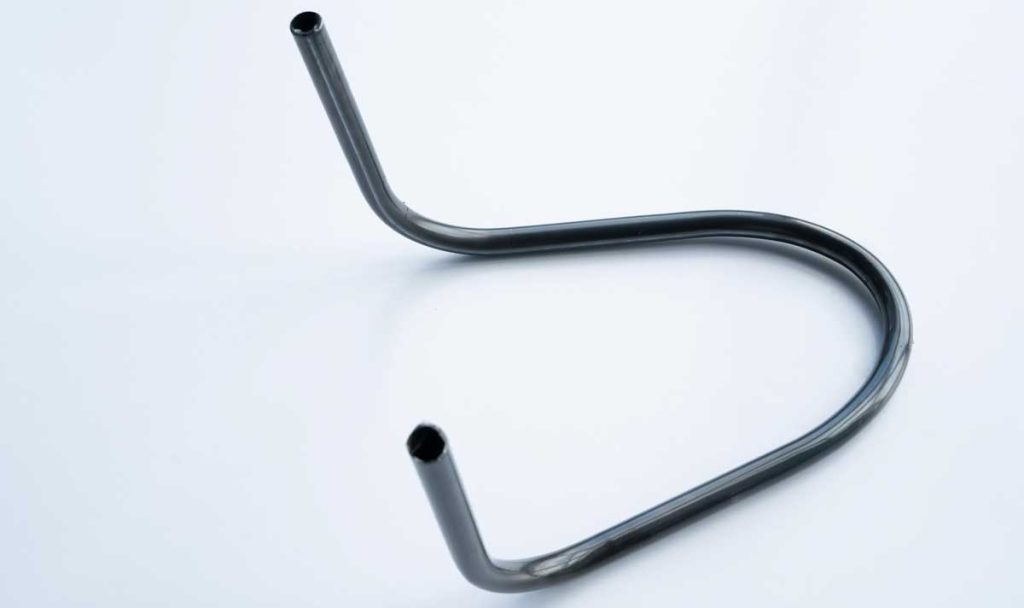
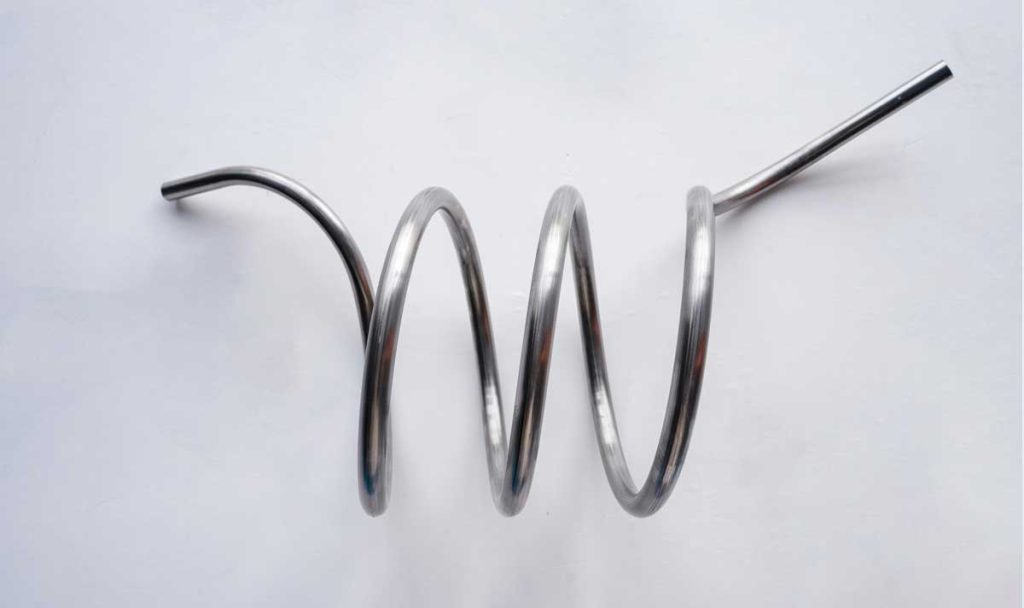
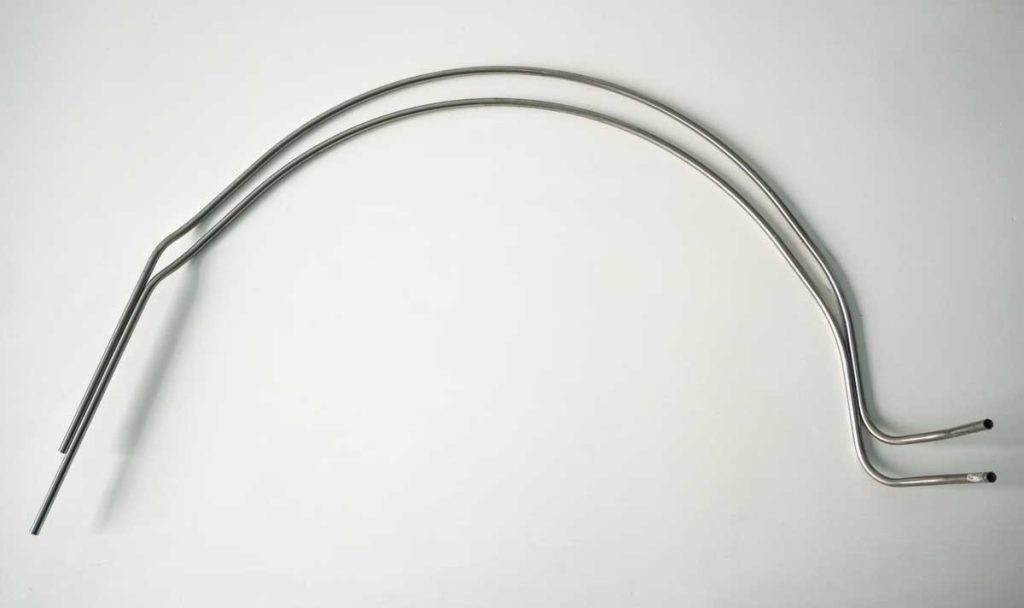
TECHNICAL PARAMETERS 6-AXIS
Model Description: PBF-S60, "S" denotes the six-axis freeform bending system, and "60" indicates the maximum processing tube diameter of 60mm (outer diameter of the tube).
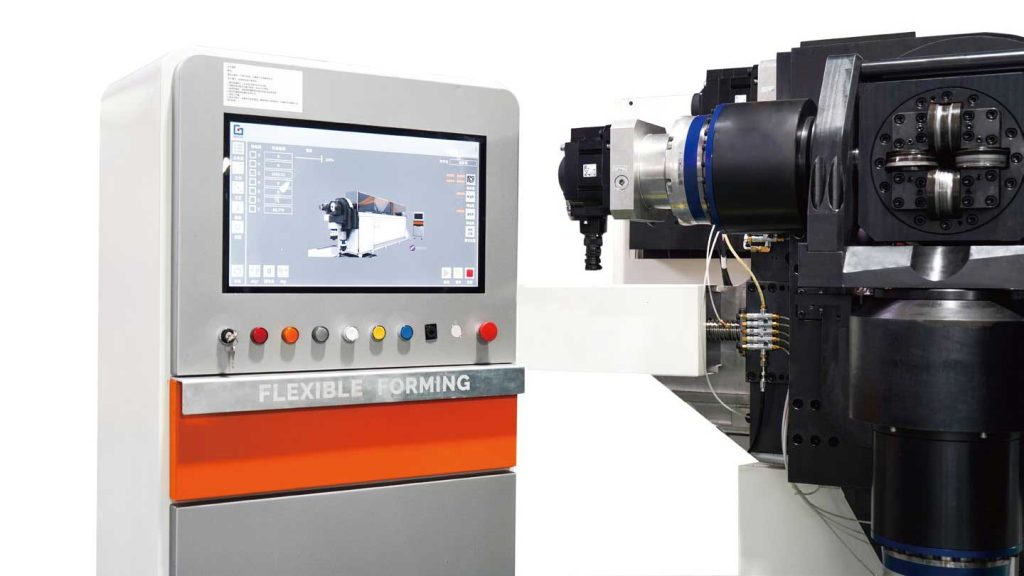
Technical Parameters | PBF-S60 | PBF-S90 |
Max Processing Tube Diameter | 30-60mm | 60-90mm |
Max Bending Radius | ∞ | ∞ |
Min Bending Radius | 3.5D | 3.5D |
Bending Angle | 0-360° | 0-360° |
Positioning Accuracy of the Feed Axis | ≤0.05mm | ≤0.05mm |
Positioning Accuracy of the Bending Axis | ≤0.02mm | ≤0.02mm |
Maximum Speed | 330mm/s | 330mm/s |
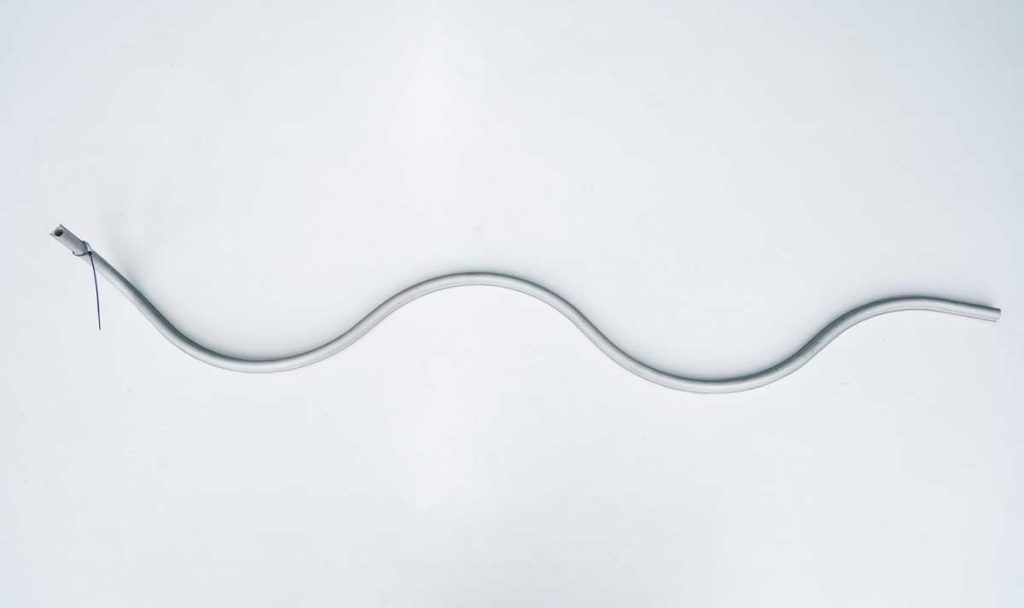
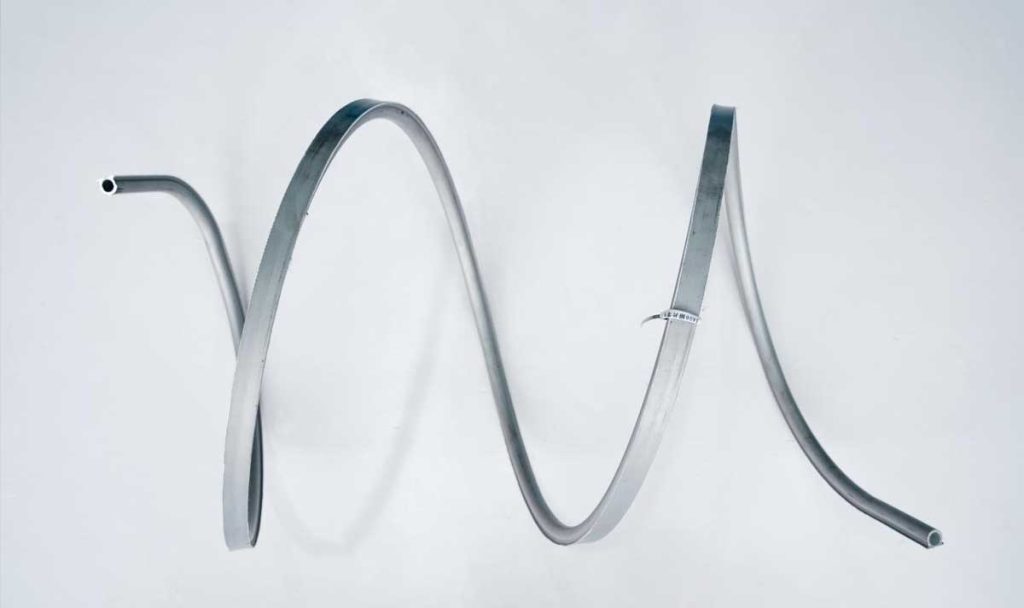
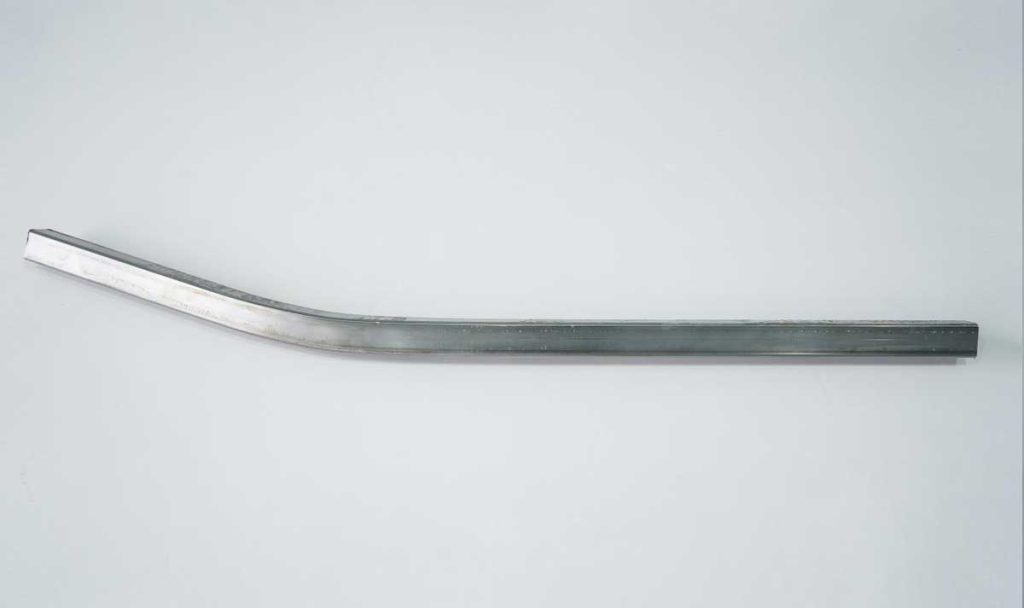
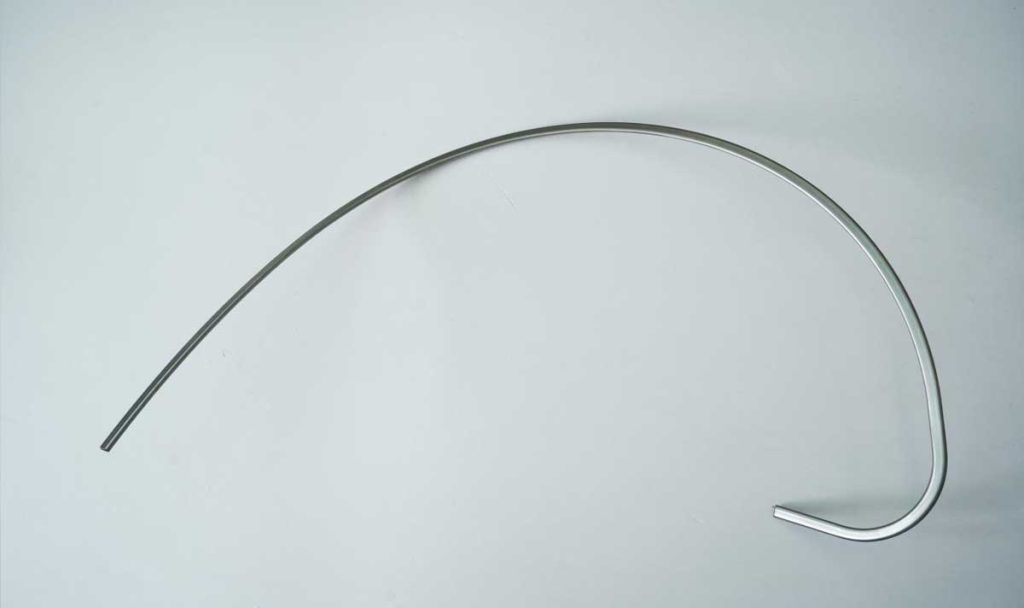
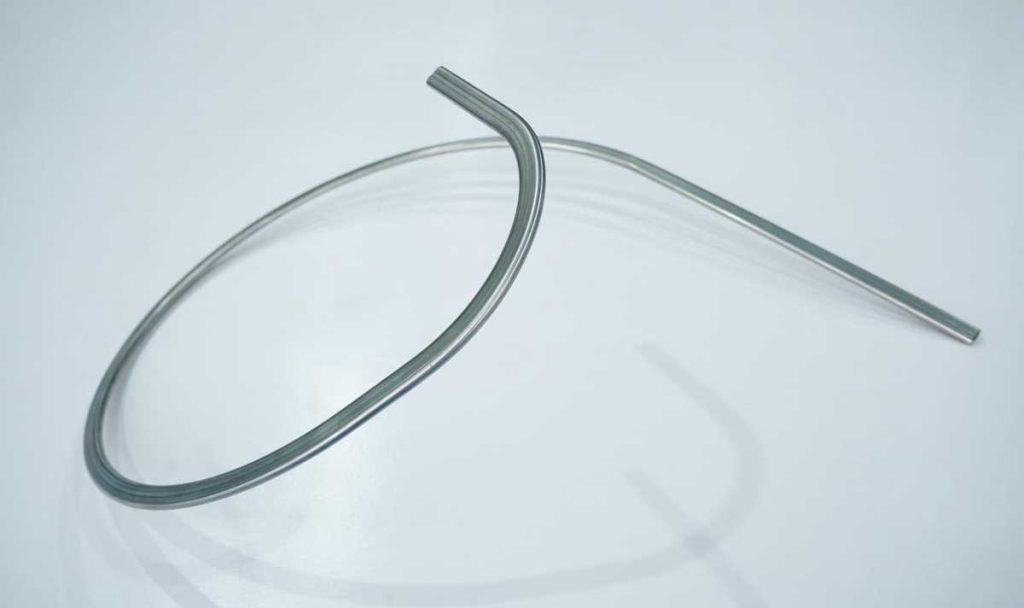
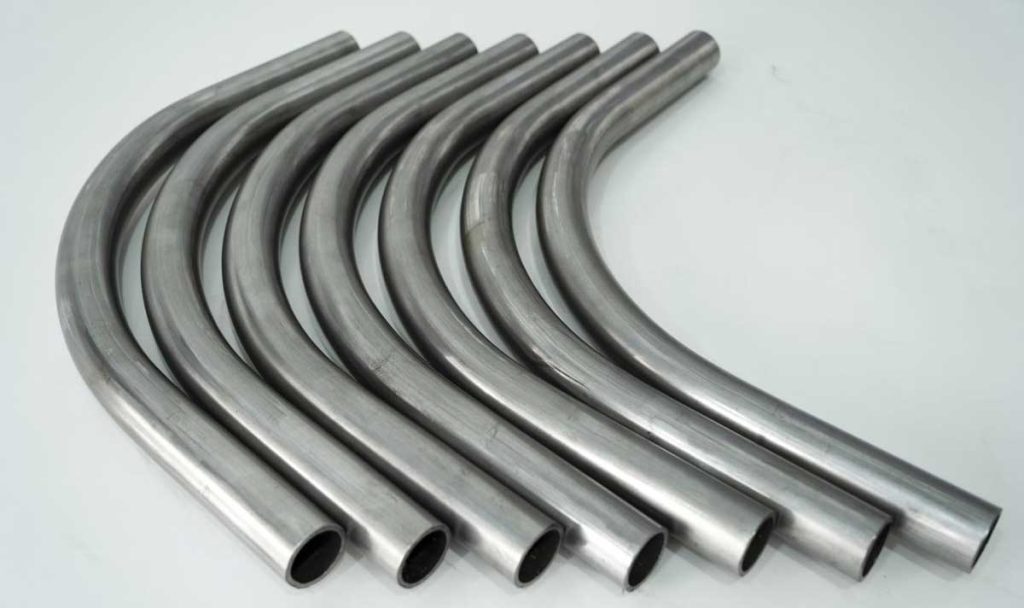
USES OF FREEFORM TUBE BENDER
The hollow bent components bent by the freeform tube bender are important components in various industrial fields.
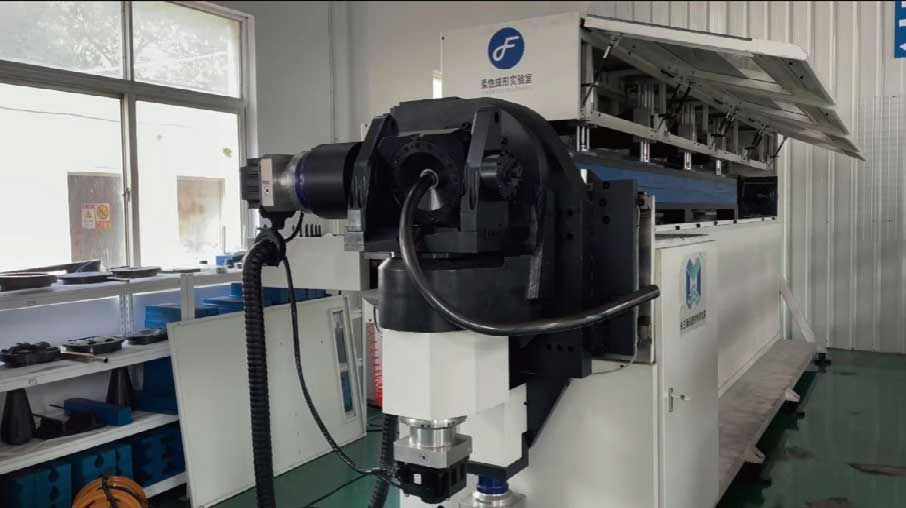
- Aerospace: Various shapes of piping systems;
- Nuclear power: Pipeline loops, steam generators, heat exchangers, condensate water supply pipelines;
- Medical: Medical devices assisting human movement;
- Building materials and decoration: Complex-shaped bent products
- Automotive: Employed in manufacturing exhaust systems, roll cages, chassis components, and other bent tubing for vehicles.
- Manufacturing: Employed in various manufacturing processes requiring complex tube bending, such as furniture production, machinery fabrication, and industrial equipment manufacturing.
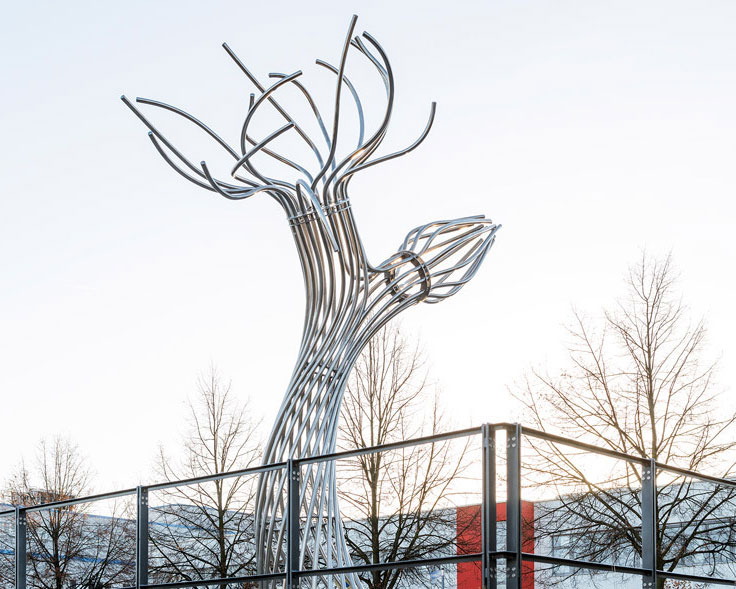
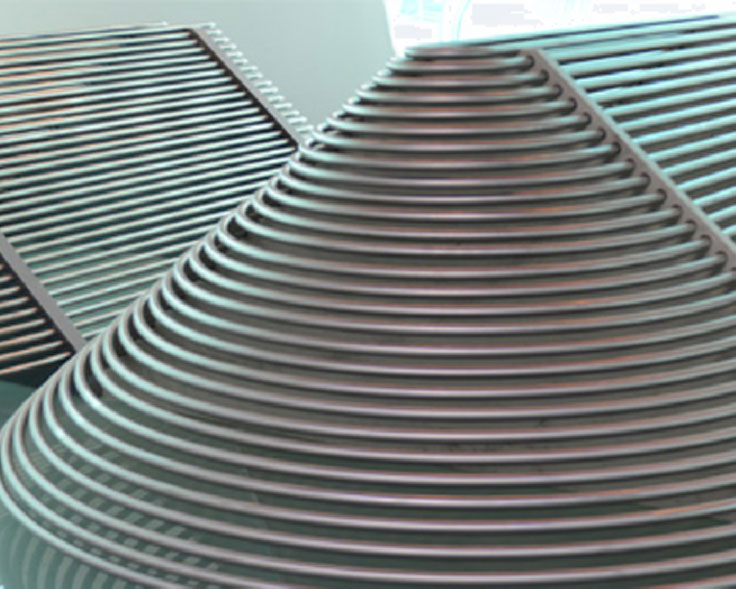
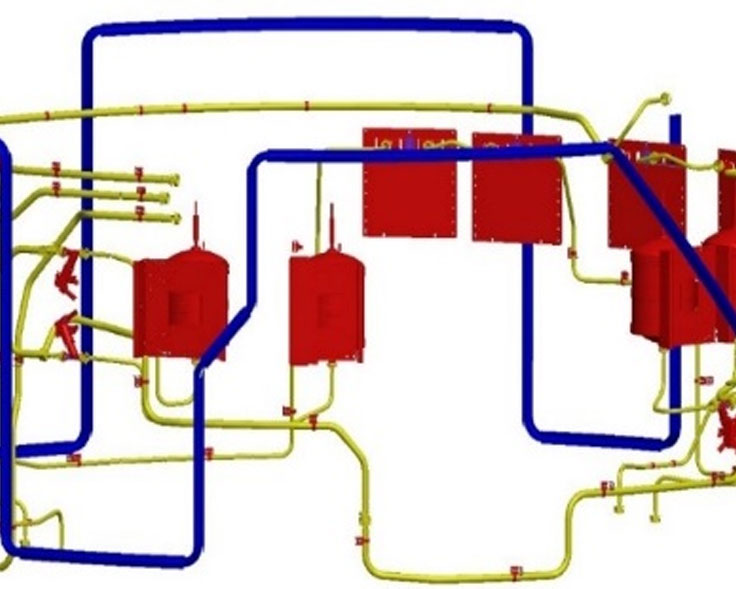
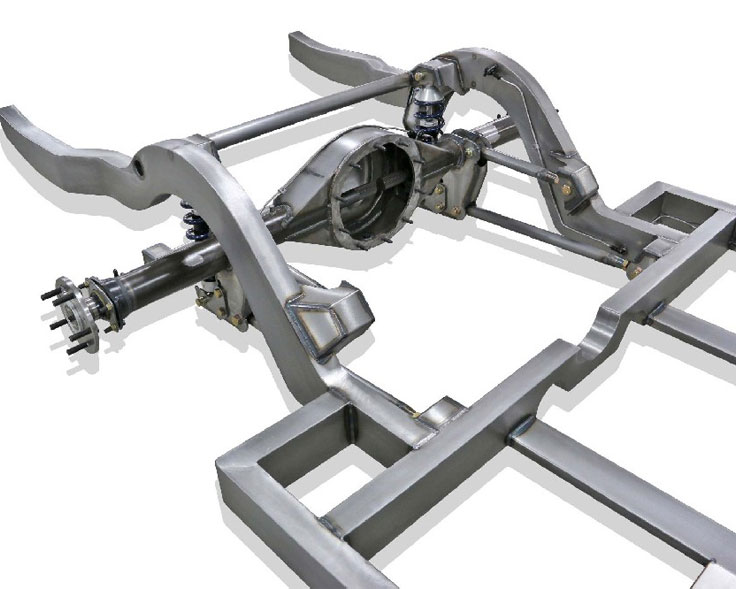
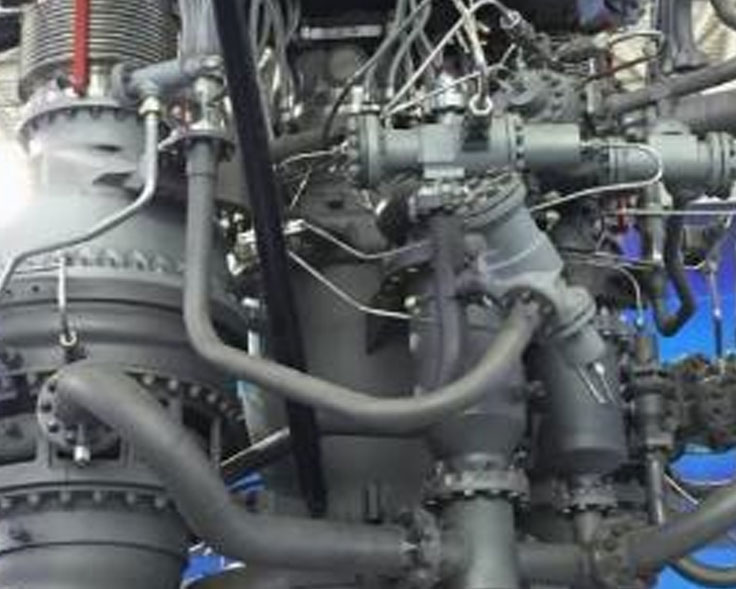
PRINCIPLE OF FREEFORM TUBE BENDER
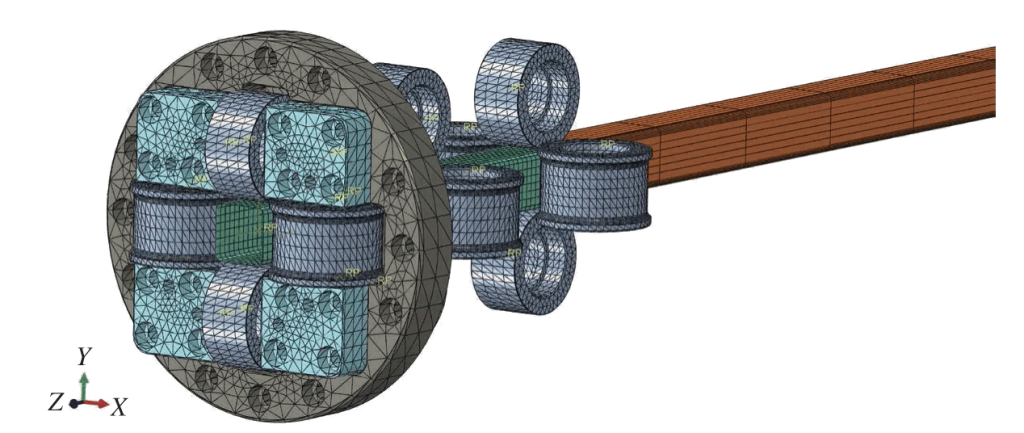
Six-axis freeform bending forming technology, as a high-degree-of-freedom manufacturing technique in the field of integral forming of complex bent components, can achieve precise overall forming of bent pipe components with complex axes and profile components with twisted cross-section characteristics.
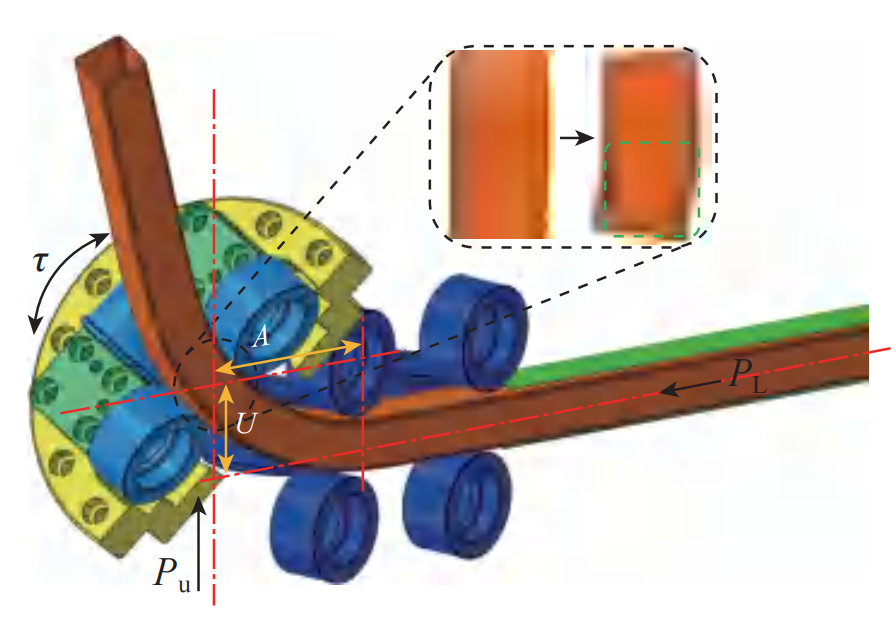
The six-axis freeform bending forming system consists of four main components: the active bending die, the guiding mechanism, the clamping mechanism, and the feeding mechanism.
Profiles are continuously pushed through the feeding mechanism, passing through the guiding mechanism and the bending die. As the profile passes through the bending die, it undergoes specific angular deviation and twisting movements in space. The distance in the vertical direction between the center point of the bending die and the center point at the exit of the guiding mechanism is called the eccentric distance U, and the distance in the horizontal direction represents the length “A” of the component’s bending and twisting deformation zone.
During the forming process, the profile is subjected to axial force PL, pushing it into the bending die, while the bending die applies a force Pu perpendicular to the feeding direction and a twisting force τ around the axis. The twisting force τ generates torque T, causing the profile to twist, with the magnitude of torque T determined by the motor parameters of the twisting axis and the material properties and cross-sectional shape of the formed profile. Under the action of Pu and PL, bending moment M is simultaneously generated, causing the profile to undergo bending deformation.
ADVANTAGES OF FREEFORM TUBE BENDER
The 7 advantages of the 3D freeform tube bender are particularly suitable for hollow components with complex spatial axes and irregular cross-sections.
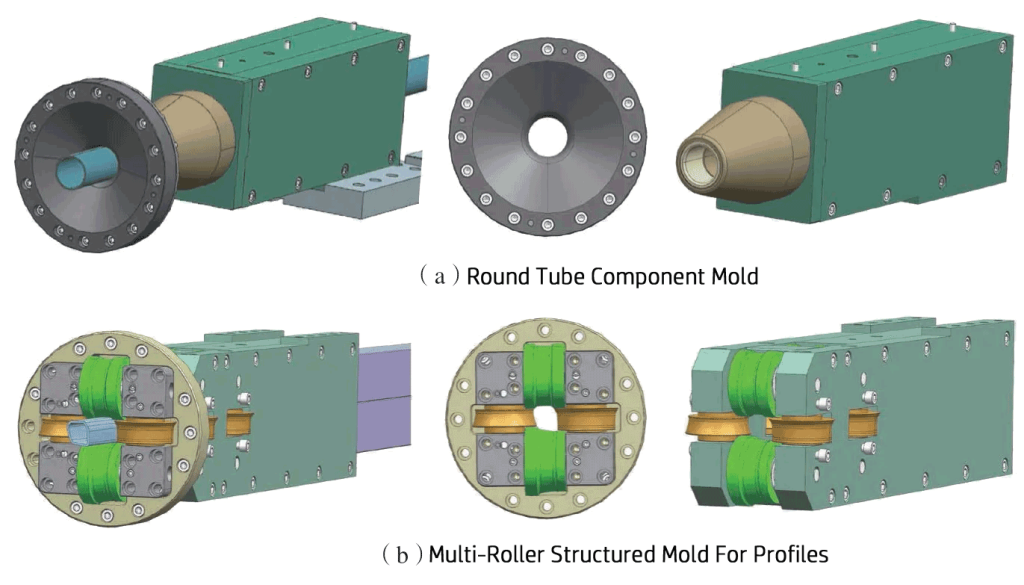
- Multi-radius Bending: Seamless bending of multi-radius workpieces.
- True Freeform Geometries: Changes in bending geometry in complex geometries can be easily accommodated, offering greater design freedom.
- High Precision: Achieve precise bending angles and dimensions, ensuring accuracy in the finished products.
- Wall Thickness: Due to the tubes being continuously pushed instead of pulled, there is almost no reduction in wall thickness at the outer bend.
- High-Quality: Even sensitive materials like aluminum and stainless steel can be bent with the highest surface quality.
- Without Molds: Bends tubes or profiles into various shapes without the need for traditional molds or dies.
- Efficiency: Freeform bending is many times faster for many bent parts than traditional methods.
About US
The Borisbang Industrial Technology (Nantong) Co., Ltd. BIT team pioneered the development of the first domestic 3D freeform tube and profile bending equipment and successfully industrialized their 6-axis freeform tube bender. They have applied for 18 invention patents, with 12 authorized, and hold 2 software copyrights.
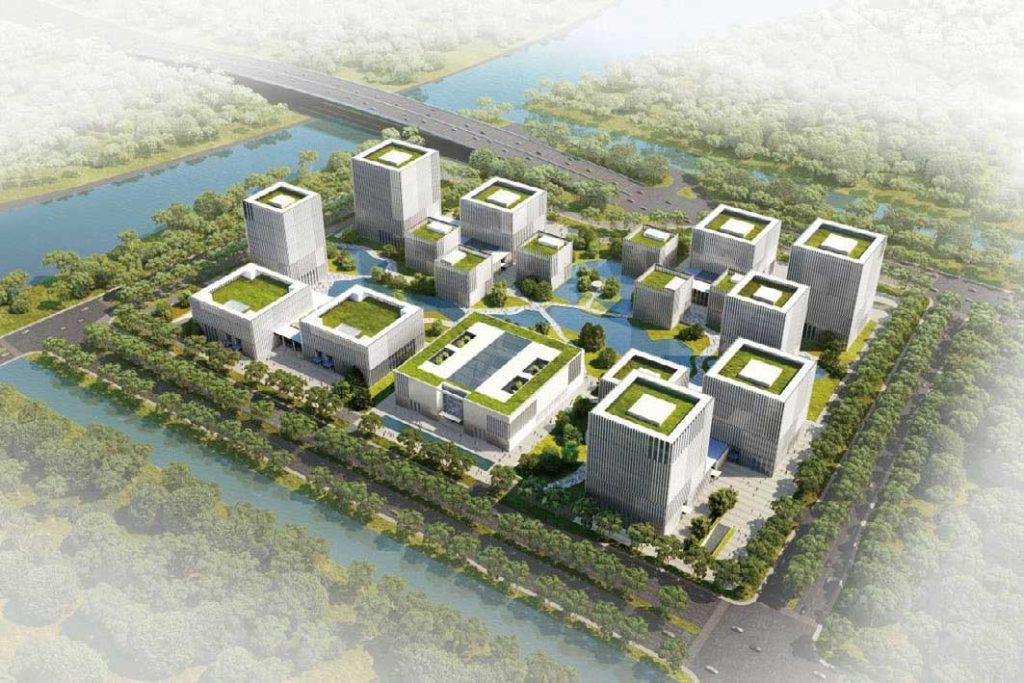
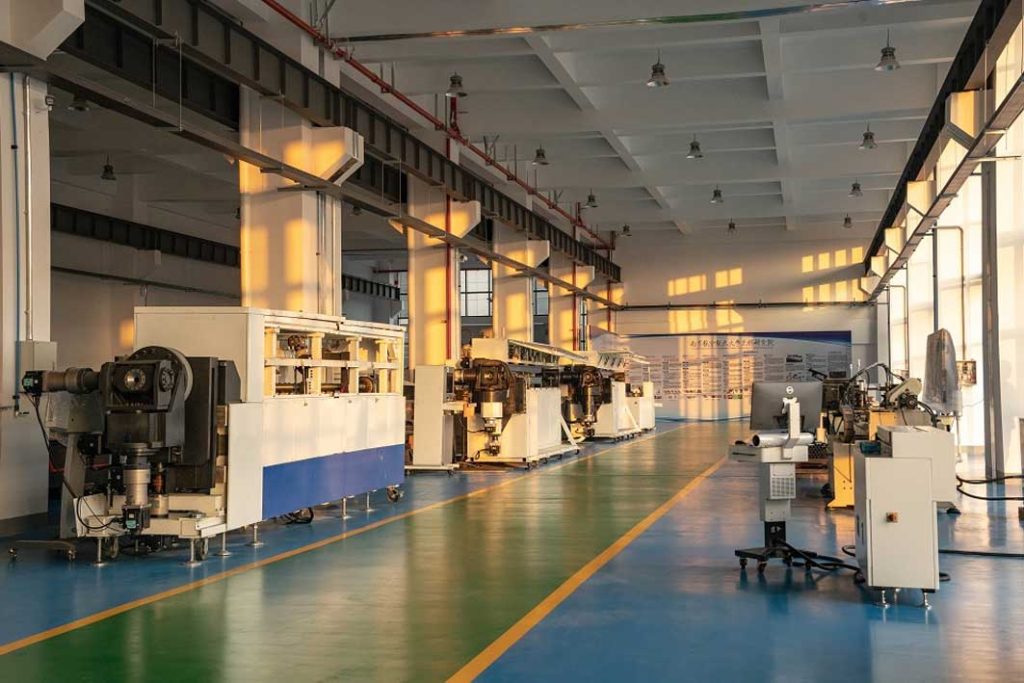
BIT Flexible Forming Team focuses primarily on researching advanced forming technologies and equipment for metals and composite materials. They have independently developed 3D Freeform Tube Bender forming equipment, numerical control progressive forming equipment, internal and external spin forming equipment, and hydraulic forming equipment. Concurrently, they conduct research on process simulation optimization, key technologies for defect control, and the preparation and forming technologies of composite components.